Prancūzijos saulės energijos institutas Ines sukūrė naujus PV modulius, turinčius termoplastiką ir natūralius pluoštus, gautus Europoje, tokius kaip linai ir bazaltas. Mokslininkai siekia sumažinti saulės baterijų aplinkos pėdsaką ir svorį, tuo pačiu pagerindami perdirbimą.
Perdirbtas stiklo skydelis priekyje ir lininis kompozitas ant nugaros
Vaizdas: Gd
Iš PV žurnalo Prancūzija
Prancūzijos Nacionalinio saulės energijos instituto (INES) tyrėjai-prancūzų alternatyvių energijų ir atominės energijos komisijos (CEA) padalinys-kuria saulės modulius, kuriuose yra naujos biologinės medžiagos priekinėje ir galinėse pusėse.
„Kadangi anglies pėdsakas ir gyvavimo ciklo analizė dabar tapo esminius kriterijus renkantis fotoelektrines plokštės, medžiagų tiekimas per ateinančius kelerius metus taps esminiu elementu Europoje“,-sakė Anis Fouini, CEA-KES direktorius. , interviu su „PV Magazine France“.
Tyrimų projekto koordinatorė Aude Derrier teigė, kad jos kolegos apžvelgė jau esančias medžiagas, kad būtų galima rasti tokią, kuri galėtų leisti modulių gamintojams gaminti skydus, gerinančius našumą, ilgaamžiškumą ir kainą, tuo pačiu sumažinant poveikį aplinkai. Pirmąjį demonstratorių susideda iš heterojunkcijos (HTJ) saulės elementų, integruotų į visos kompozitinę medžiagą.
„Priekinė pusė pagaminta iš stiklo pluošto užpildyto polimero, kuris užtikrina skaidrumą“,-teigė Derrier. „Galinė pusė pagaminta iš kompozito, pagrįstos termoplastiku, kai buvo integruotas dviejų pluoštų, linų ir bazalto audimas, kuris užtikrins mechaninį stiprumą, bet taip pat geresnį atsparumą drėgmei“.
Lenas gaunamas iš Šiaurės Prancūzijos, kur jau yra visa pramonės ekosistema. Bazaltas gaunamas kitur Europoje ir austas pramoninio Ines partnerio. Tai sumažino anglies pėdsaką 75 gramais CO2 vienam vatui, palyginti su tos pačios galios pamatiniu moduliu. Svoris taip pat buvo optimizuotas ir yra mažesnis nei 5 kilogramai kvadratiniam metrui.
„Šis modulis skirtas stogo PV ir pastatų integracijai“, - sakė Derrier. „Privalumas yra tas, kad jis yra natūraliai juodos spalvos, nereikalaujant užpakalinio lapo. Kalbant apie perdirbimą, dėka termoplastikų, kuriuos galima perdaryti, sluoksnių atskyrimas taip pat yra techniškai paprastesnis. “
Modulį galima pagaminti neįregistruojant dabartinių procesų. Derrier teigė, kad idėja yra perkelti technologijas gamintojams be papildomų investicijų.
„Vienintelis imperatyvas yra turėti šaldiklius, kad būtų galima laikyti medžiagą ir nepradėti dervos kryžminio sujungimo proceso, tačiau dauguma gamintojų šiandien naudojasi„ Prepreg “ir jau yra tam pasirengę“,-sakė ji.
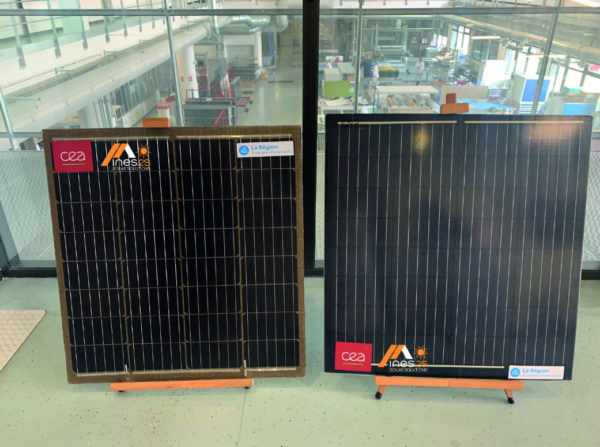
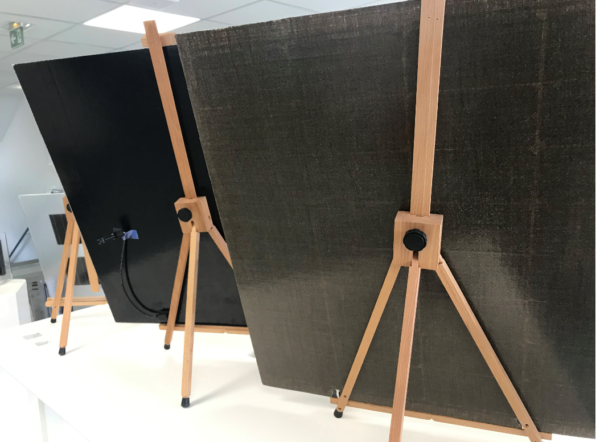
„Mes dirbome prie antrojo stiklo gyvenimo ir sukūrėme modulį, sudarytą iš pakartotinai panaudoto 2,8 mm stiklo, kilusio iš seno modulio“, - sakė Derrier. „Mes taip pat naudojome termoplastinį kapsulę, kuriam nereikia kryžminio sujungimo, todėl bus lengva perdirbti, ir termoplastinis kompozitas su linų pluoštu, kad būtų atsparumas.“
Galiniame modulio galiniame veide be bazinės spalvos yra natūrali skalbinių spalva, kuri, pavyzdžiui, gali būti estetiškai įdomi architektams. Be to, INES skaičiavimo įrankis parodė, kad anglies pėdsakas sumažėjo 10%.
„Dabar būtina abejoti fotoelektrinių tiekimo grandinėmis“, - sakė Jouini. „Padedami Rhône-Alpes regiono pagal Tarptautinio vystymosi plano rėmus, mes ieškojome žaidėjų, esančių už saulės sektoriaus ribų, kad surastume naują termoplastiką ir naujus pluoštus. Mes taip pat galvojome apie dabartinį laminavimo procesą, kuris reikalauja daug energijos. “
Tarp slėgio, presavimo ir aušinimo fazės laminavimas paprastai trunka nuo 30 iki 35 minučių, o darbinė temperatūra yra maždaug 150–160 c.
„Tačiau moduliams, kuriuose vis dažniau yra ekologinių medžiagų, būtina transformuoti termoplastiką maždaug nuo 200 C iki 250 C, žinant, kad HTJ technologija yra jautri šilumai ir neturi viršyti 200 C“,-sakė Derrier.
Tyrimų institutas bendradarbiauja su Prancūzijoje įsikūrusios indukcinės terokompresijos specialistu „Roctool“, kad sumažintų ciklo laiką ir sudarytų formas pagal klientų poreikius. Kartu jie sukūrė modulį su galiniu veidu, pagamintu iš polipropileno tipo termoplastinio kompozito, kuriam buvo integruota perdirbtų anglies pluoštų. Priekinė pusė pagaminta iš termoplastikos ir stiklo pluošto.
„„ Roctool “indukcinio terokompresijos procesas leidžia greitai įkaitinti abi priekines ir galines plokšteles, nereikia pasiekti 200 C HTJ ląstelių šerdyje“, - teigė Derrier.
Bendrovė teigia, kad investicijos yra mažesnės, o procesas gali pasiekti vos kelių minučių ciklo laiką, tuo pačiu sunaudojant mažiau energijos. Ši technologija skirta kompoziciniams gamintojams, kad suteiktų galimybę gaminti įvairių formų ir dydžių dalis, kartu integruojant lengvesnes ir patvaresnes medžiagas.
Pašto laikas: 2012 m. Birželio 24 d